Our Process
AN APPROACH UNLIKE ANY OTHER
AMI delivers fast, dependable installations of self-checkout systems, POS terminals, and other in-store retail tech—so your business keeps running without missing a beat. Our full-time technicians work efficiently, often after hours, to avoid disrupting your day-to-day operations.
Beyond the install, we offer full smart cash management rollouts, GIS mapping, real-time project updates via API, and cloud-based tracking tools. From site surveys to IT integration and staff training, AMI handles it all—making sure your project is done right, on time, and with zero hassle.
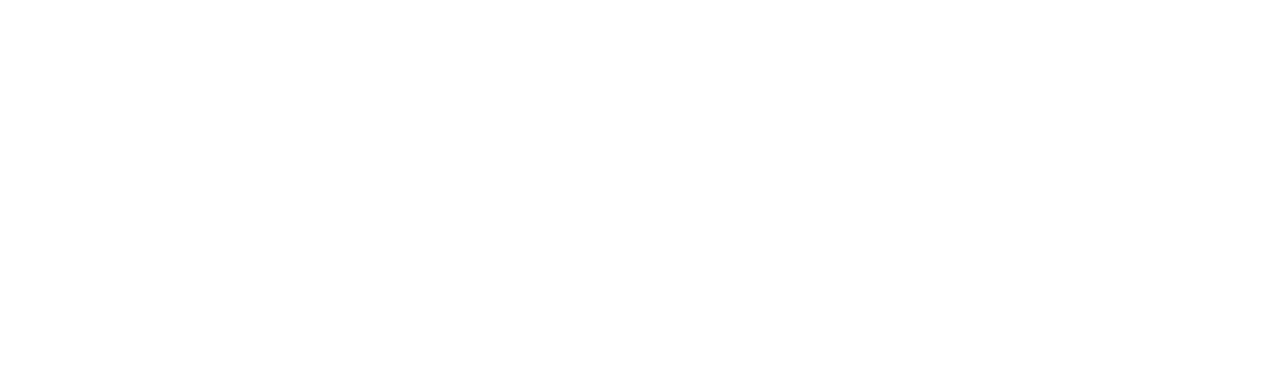
ADVANCED MATERIAL INSTALLATION
Our Process
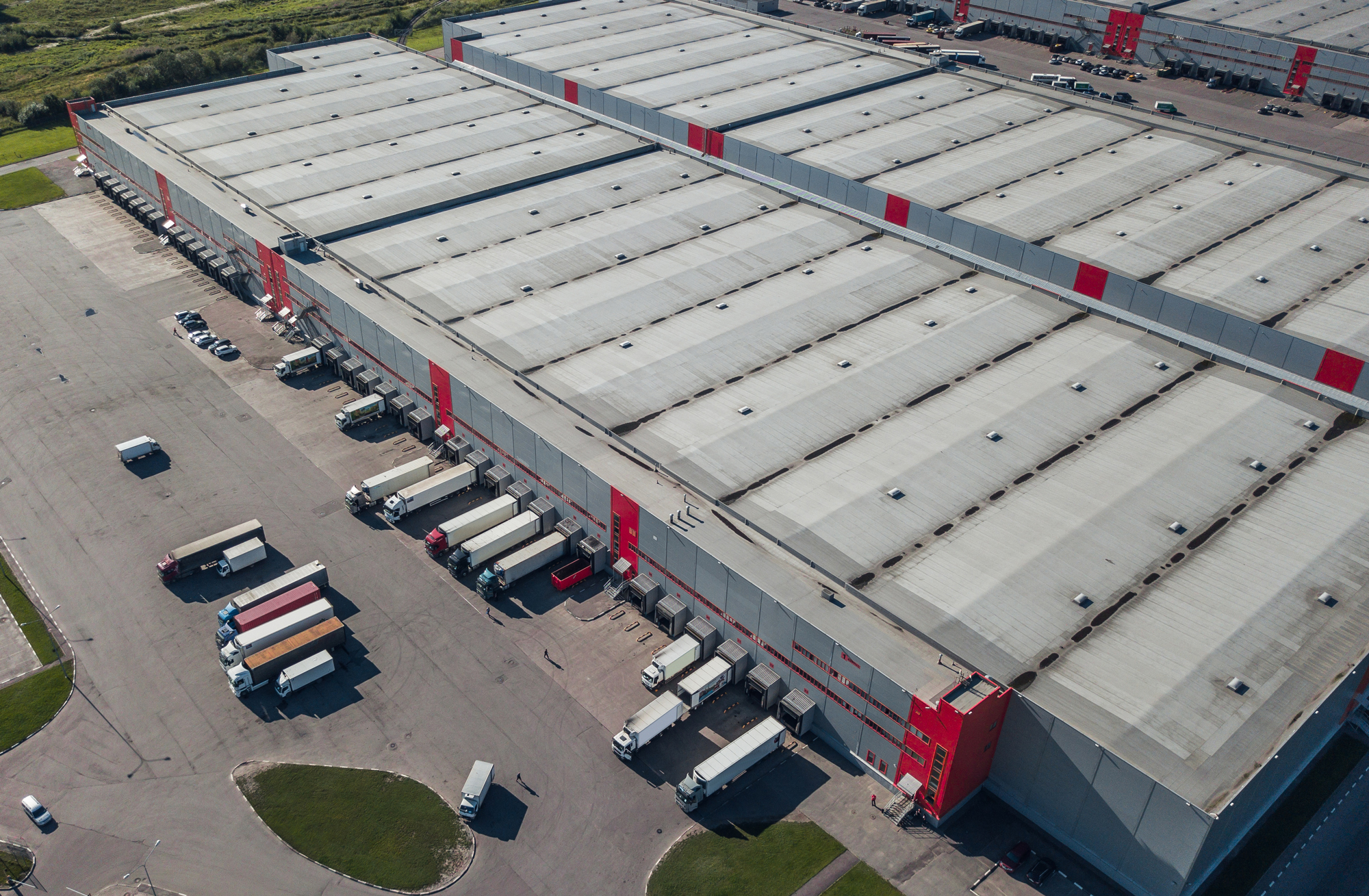
Strategic Logistics
AMI’s extensive warehouse network and customized distribution plans ensure timely, cost-effective equipment delivery nationwide.
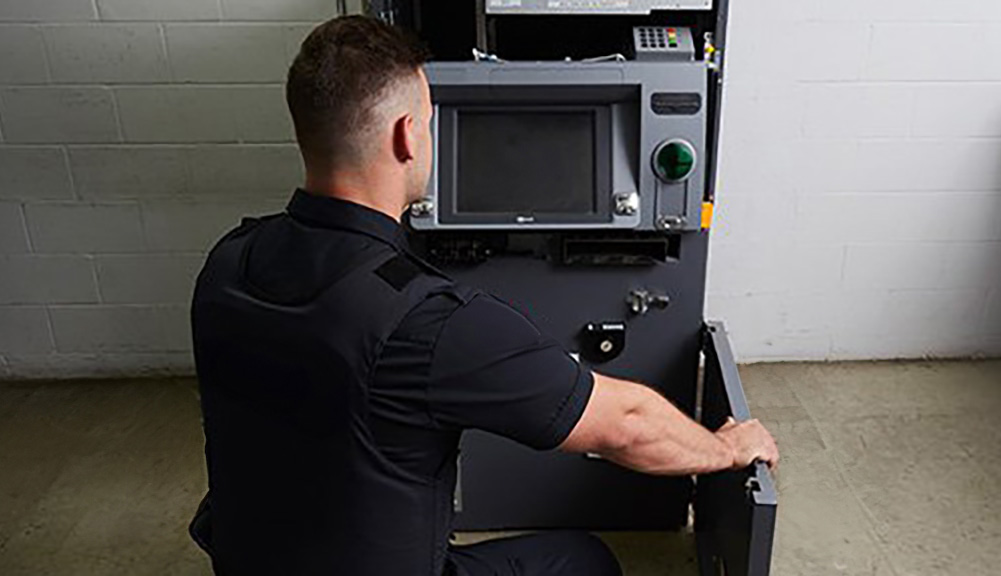
Expert Installations
Our in-house technicians provide comprehensive installations, handling all aspects to deliver turnkey solutions.
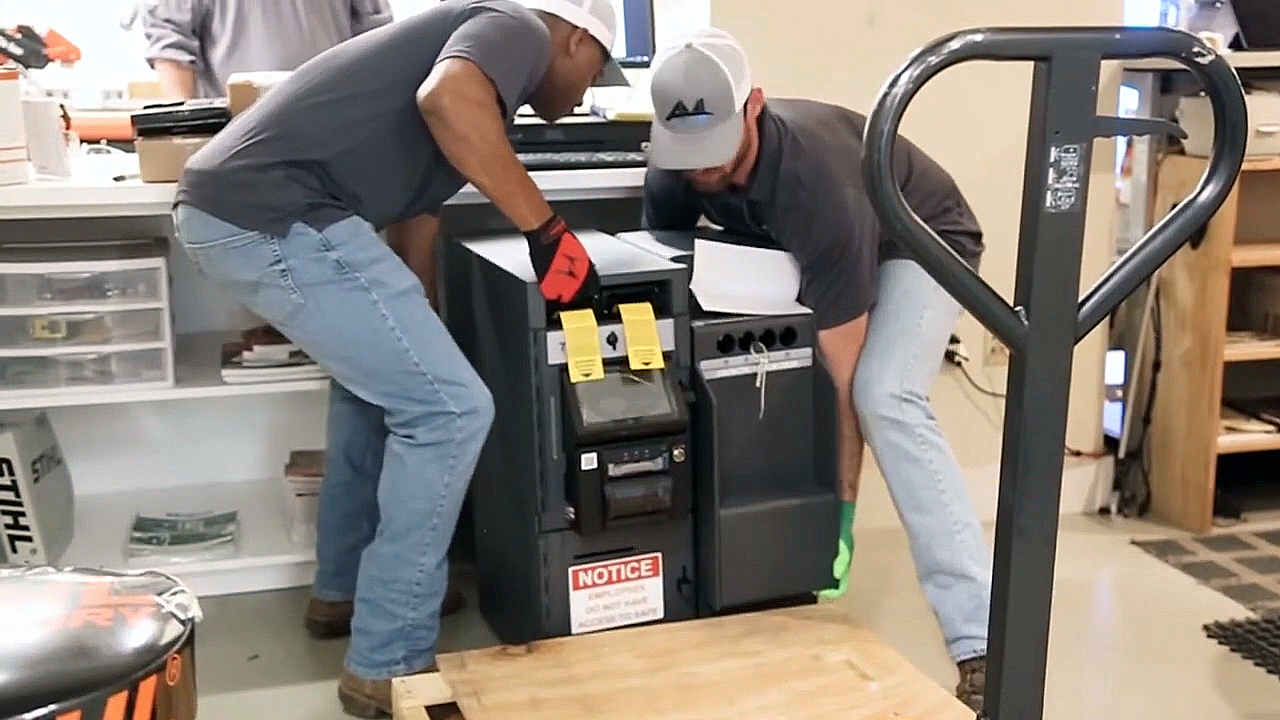
RESPONSIBLE REMOVALS
We efficiently remove and dispose of outdated equipment, adhering to all local regulations and minimizing disruption.
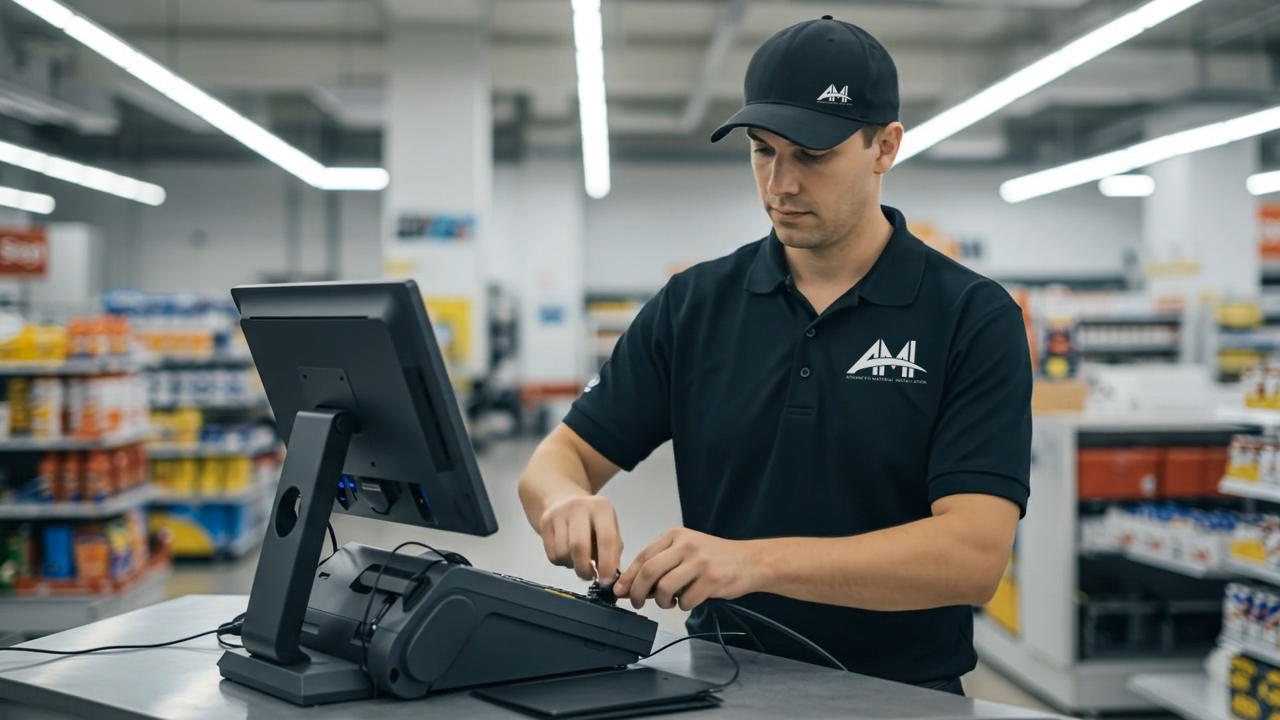
Precise Setup
Using Smartsheets alongside our mobile data platform, we program and commission equipment with precision—ensuring it’s fully operational and ready for immediate use.
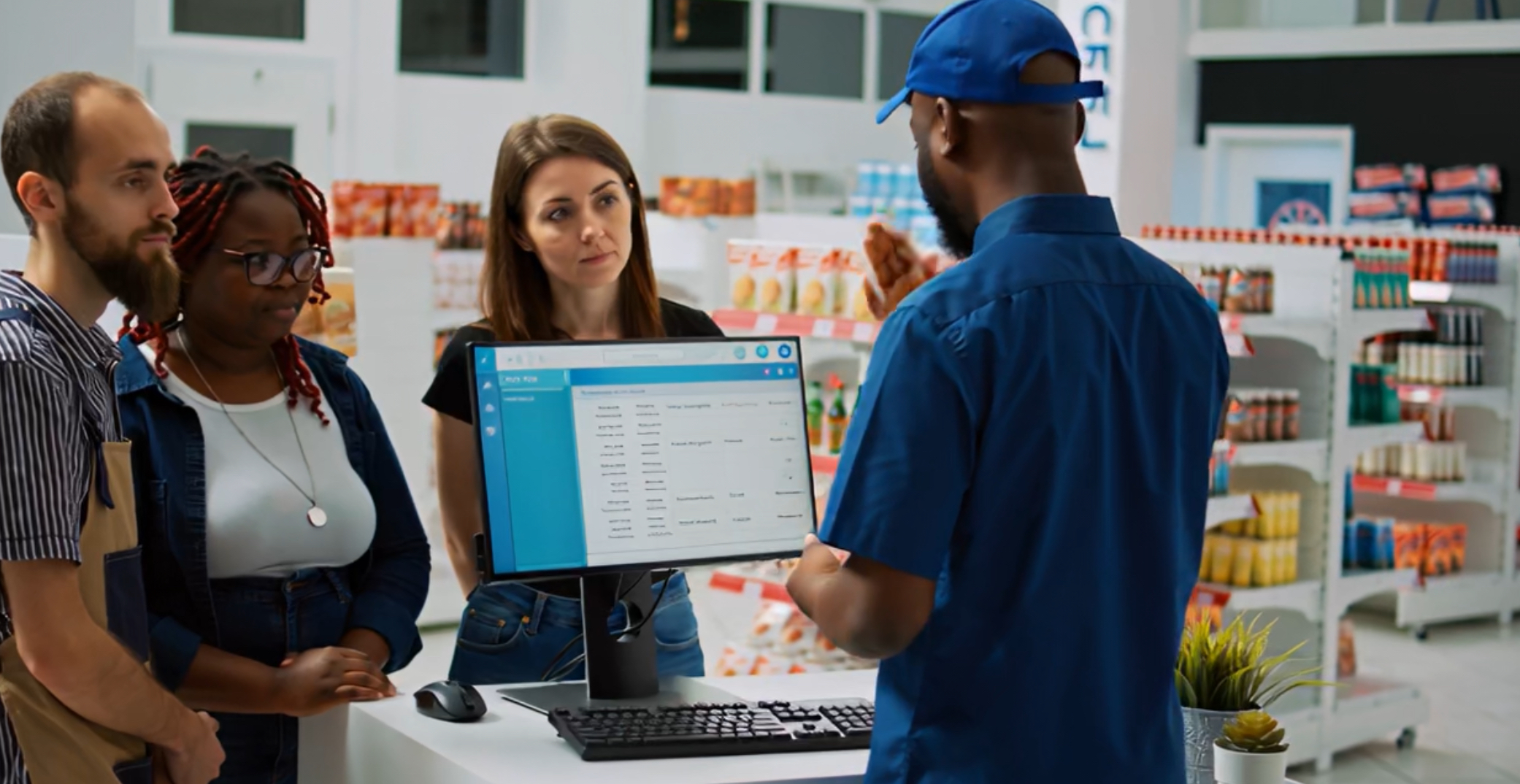
Comprehensive Training
Our training programs empower your staff to operate new systems confidently, with ongoing support as needed.
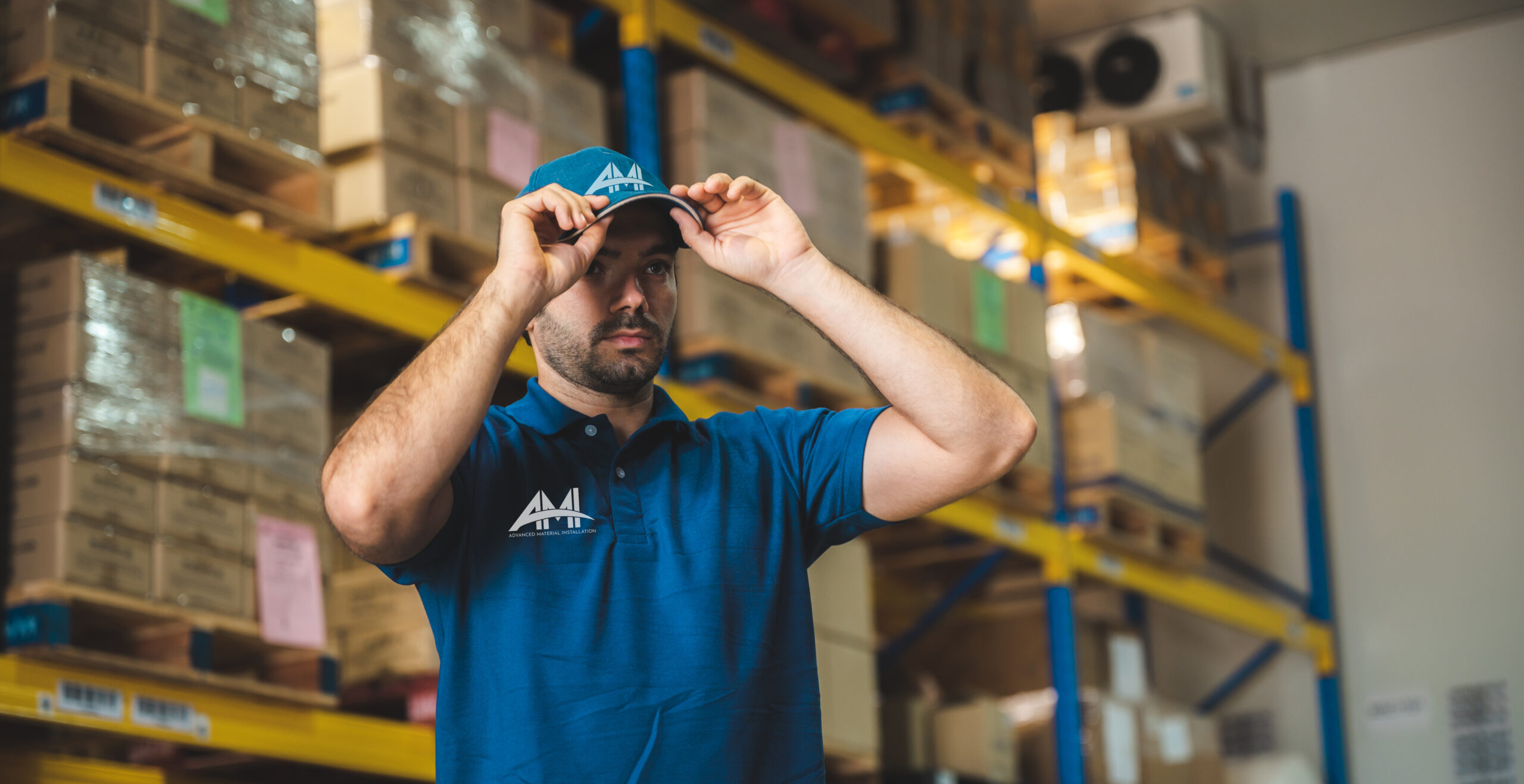
Proven Track Record
Trusted by industry leaders, Advanced Material Installation delivers reliable, high-quality installations tailored to each client’s unique needs.
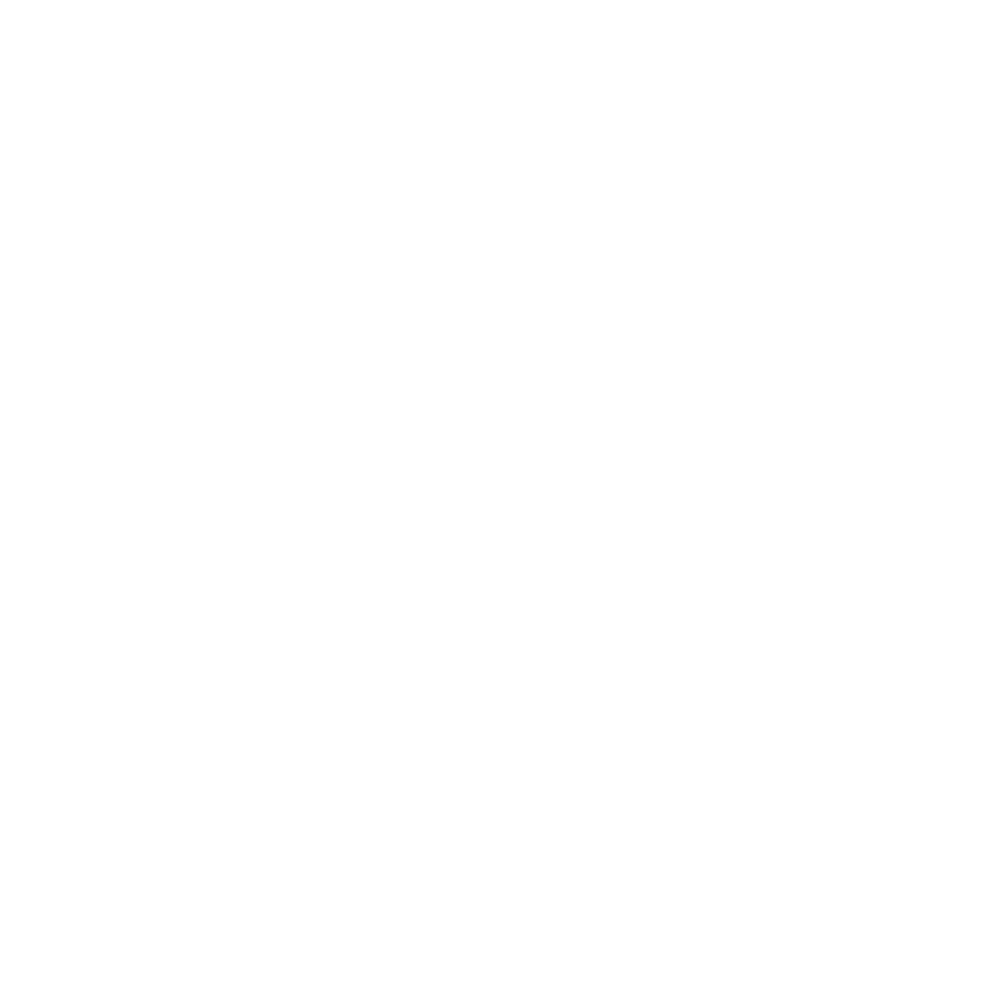
THE PREMIER INSTALLATION & PROJECT MANAGEMENT COMPANY
Advanced Material Installation
DIFFERENTIATORS
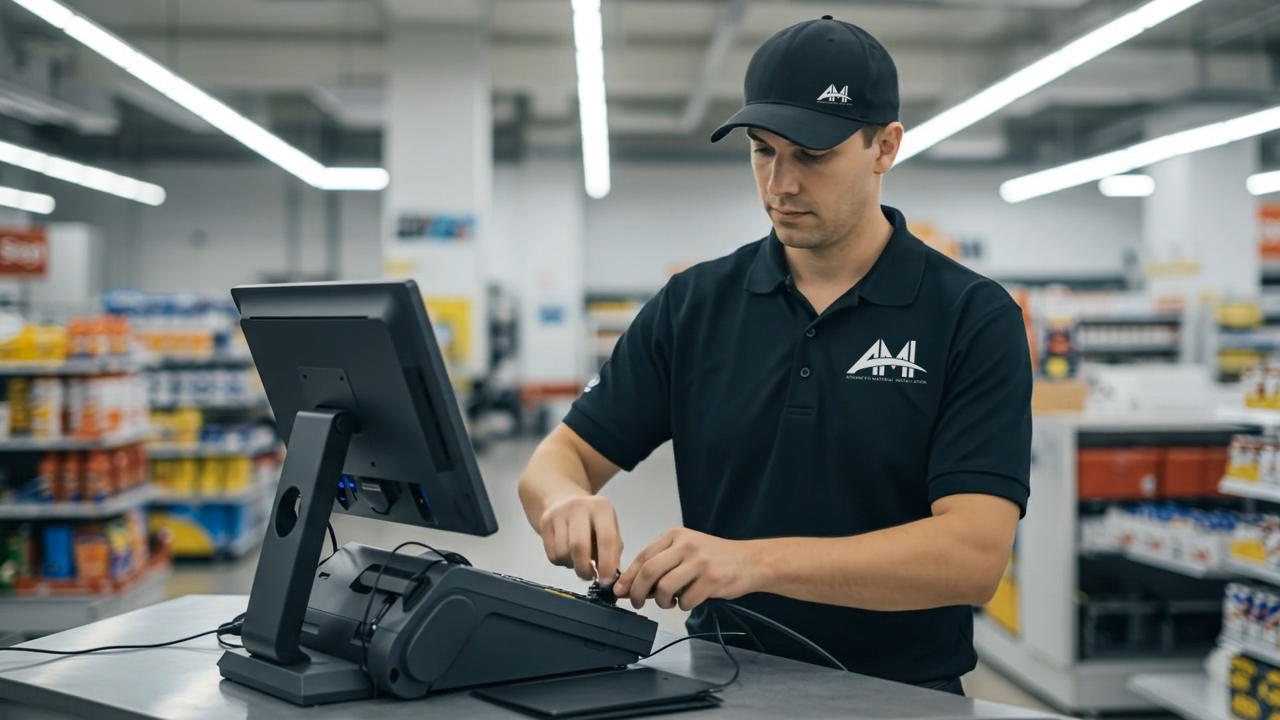
Reduced Disruption:
We provide flexible scheduling, including the option to work after regular business hours, so your operations aren’t disrupted. Our site surveys further support this by identifying potential challenges in advance—allowing for better planning and smoother installations that don’t interfere with staff, customers, or daily workflows.
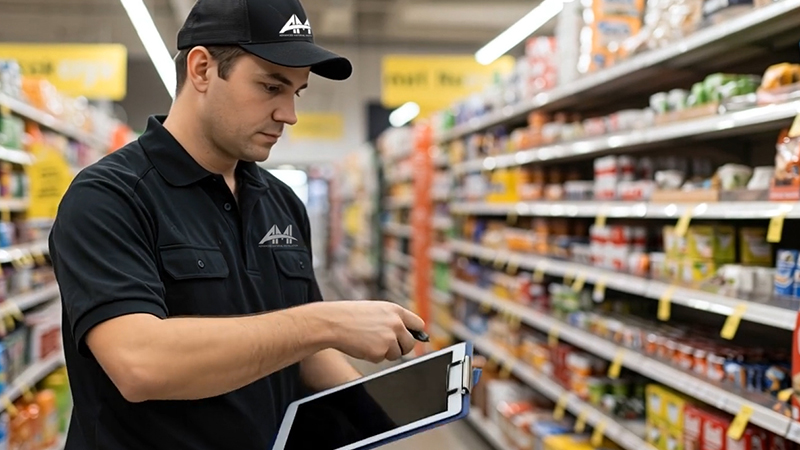
Improved ROI
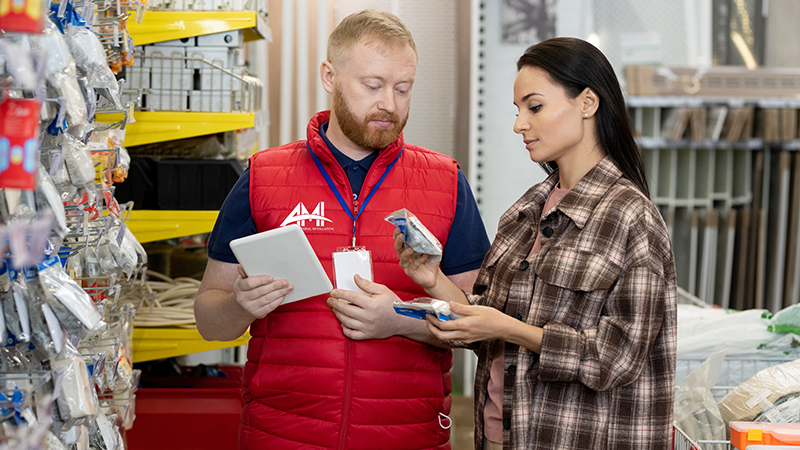
Seamless Data
With Smartsheets-enabled custom integrations, we seamlessly connect to your systems—transforming data into clear, actionable insights that support smarter decision-making. Our site surveys feed directly into this planning process, capturing key details early to ensure accurate execution from day one.
Advanced Material Installation Case Studies
Nationwide Smart Safe Rollout for Deposita
-
Challenge: Deploy smart safes across 200+ retail locations in 12 weeks.
-
Solution: AMI’s traveling technicians and mobile data platform ensured on-time delivery with real-time updates.
-
Result: Completed in 12 weeks, saving Deposita 15% on project management costs.